Innovative and collaborative robotics
Robotics as a competitive advantage. We help customers solve labor shortages, increase productivity, and improve product quality with sustainable, flexible, and safe smart manufacturing applications.
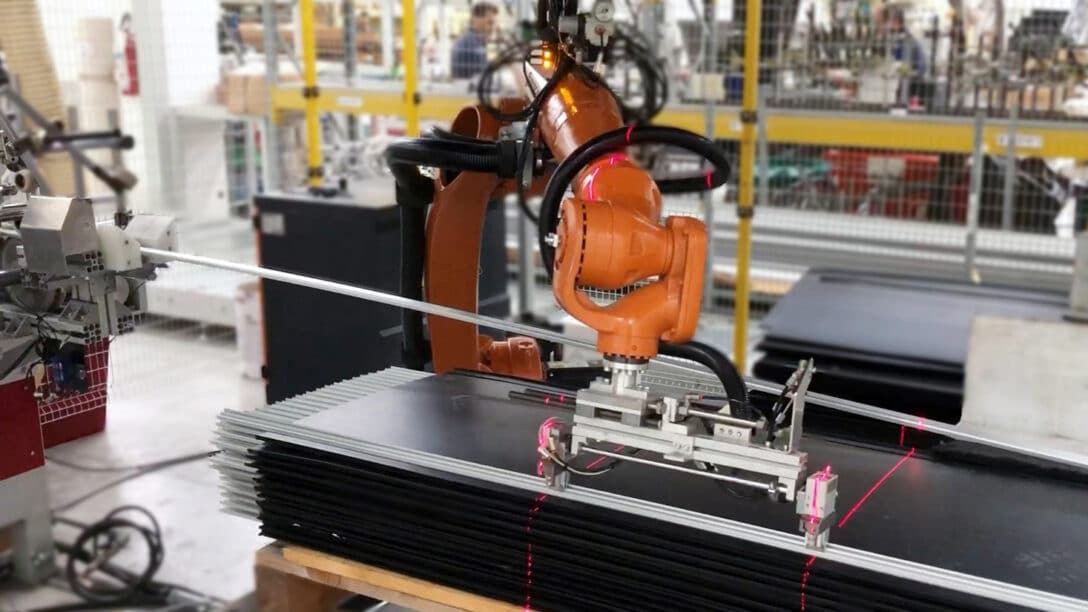
Robotics as a competitive advantage.
We design and implement robotic lines and cells according to specific customer requirements, employing robots from the best-known brands, particularly ABB, Kuka, Comau, Omron, and Universal Robot.
Agile, versatile, and easy to program, industrial robots are now indispensable working tools for automating the plants of the future. This is why Carretta collaborates with manufacturing companies, system integrators, and researchers to develop “user experiences” and propose new robotic applications in manufacturing processes.
- Robots with vision systems for guiding, inspection, defect detection, alignment, and measurement.
- Implementation of kinematics suitable for different automation requirements: scara, delta, and anthropomorphic.
- Robots with random bin picking applications for randomly arranged object picking.
- Collaborative robot applications are the smart manufacturing environments where operators and cobots work together in unison.
Cobot: collaborative robots
The Cobot, short for COllaborative and roBOT, is a robot designed for direct interaction with humans within a defined collaborative workspace. For flexibility of use and safe direct interaction with the operator, it opens up revolutionary scenarios for the competitiveness of SME manufacturing.
Cobots: what they are and how they work
Compared with traditional industrial robots, Cobots are extremely compact and lightweight but most importantly designed to interact with people.
This translates to ergonomics and advanced safety-native features for robotic equipment that do not require protective cages: cobots respect safe distances between each other and between operators, even going so far as to slow down as people enter the area of action and stop at the slightest contact. Intervals and stopping trajectories are programmable and customizable thus ensuring operational versatility. Another defining aspect of advanced manufacturing is the high motion and positioning accuracy achieved by today’s cobots.
What can be automated? Discover it step by step!
Typically, a Cobot is successfully employed to help operators with repetitive, monotonous, or hazardous manual tasks, non-skill-based activities that do not require any specific decision-making processes.
The suggested tasks for collaborative robotics generally include:
- Repetitive tasks that do not require force exerted by the robot, such as picking up, placing, and depositing an object on a surface.
- Processes are performed on parts similar to each other in size and shape, such as items placed in a predetermined manner on a table.
- Tasks that require interaction with a fixed object.
- Processes are based on picking up and placing objects always in the same position.
The following is a brief step by step guide to suggest setting up collaborative equipment in manufacturing environments.
Speed of task execution approaches that of the human operator.
It is recommended to implement a collaborative robot if you are looking for increased productivity with multiple shifts or 24h/24h or if you want to assist the worker in repetitive, sequential, low-value-added tasks.
Simple | Complex |
---|---|
Low volumes | Large batches |
High mix | More workers when production increases (higher risk conditions) |
If the production speed is similar to that of human workers |
Generally, collaboratives are suitable for narrow spaces, with an arm reach of less than 1300 mm, and for handling payloads up to 16 kg (including the weight of the grapple at the end of the arm).
Their compact nature allows them to perform tasks in areas with limited space.
Simple | Complex |
---|---|
Payload up to 10 kg | Payload is between 10 and 35 kg |
Arm reach: 500-900 mm | Arm reach: 1300-1600 mm |
If multiple Cobots are on a single workstation | |
If the collaborative robot is two-armed |
Cobots prefer workpieces with footprints and surfaces with good uniformity. To simplify implementation, orderly and repeatable access to parts is preferred (usually on a table or tray so that the process can be replicated without resorting to sophisticated programming).
It is possible to set up the ordered “matrix” parts (support jigs) by configuring the cobot on the pickup-deposit sequence.
Simple | Complex |
---|---|
If there are sequential operations with a clear separation between cobot and operator operations | If there are imaging systems or sensors to identify and pick up parts |
If there are basic commands such as start-cycle and end-cycle | If the picking is random from a bin |
If there are uniform dimensions and sizing | |
If there is an orderly presentation of parts |
Even though Cobots are designed to work safely alongside workers, they require a pre-implementation study with a focus on specific “collaborative applications”.
This is because risk analysis is required upstream in the design phase, taking into account that each application is different and stand-alone, with its features that make a generic analysis of all robots in all work contexts ineffective.
It is good practice to assign repetitive, manual, and potentially life-threatening tasks and sequences to the robot, and to devote tasks to the operator that enhance his or her skills and abilities – such as supervisory tasks -.
Levels of engagement between humans and robots based on sharing time and space
- The operator and robot operate in environments separated by physical barriers (cell).
- The operator and cobot operate in the same environment but do not interact with each other (coexistence).
- The operator and cobot operate in the same workspace but alter in occupying it (synchronization)
- The operator and cobot operate in the same workspace simultaneously but on different tasks (cooperation)
- The operator and cobot perform the task together, the actions of one affecting the other (cooperation)
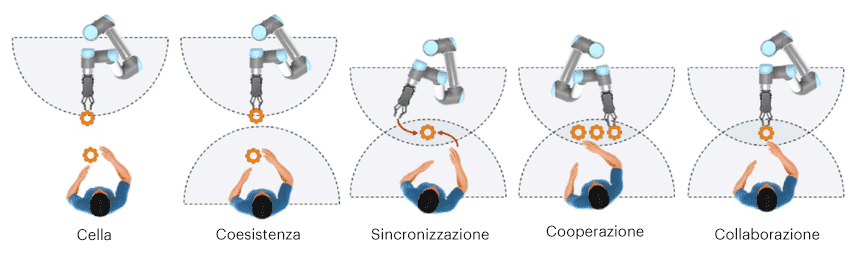
It is critically important to consider the type of interaction needed:
- simple collaborative robotics with tasks such as loading/unloading parts, opening doors, and activating levers/buttons… in these cases, these are simple interactions that are part of 90% of cobot tasks today;
- complex collaborative robotics when, on the other hand, there is close interaction between robot and operator: alternating operator-tasks cobot tasks within a work cycle
Simple | Complex |
---|---|
If there are simple interaction operations | If there is cobot-operator interaction |
If there are operations with close human-robot interaction | If there is cobot-operator collaboration |
If there is cobot-operator synchronization |
The gripping mechanism mounted on the robotic arm used to interact with parts and machines is a key component.
The range of solutions is from standard robotic gripping solutions to electro-pneumatic devices and grippers made for a variety of handling needs such as certified grippers, long-stroke grippers, custom grippers, and gripper changing systems … which may also require additional overhaul-certification of equipment safety.
Simple | Complex |
---|---|
If standard gripping devices and tools are readily available | If they are specific grippers and tools |
If they are custom gripping solutions for multiple tasks |
Relative simplicity is achieved with Cobots installed in a dedicated mobile table.
Advanced task sequences and logistics can involve collaboratives combined with automated guided systems (AGVs): in which case an autonomous mobile robot, can dynamically navigate using a map, with planned routes within the production layout.
Simple | Complex |
---|---|
If cobot is anchored to a collaborative table | If there is a combination of Cobot to self-driving vehicles (AGV) |
Some applications require cobots with certification suitable for use in cleanrooms and sterile environments. A certification that creates the necessary conditions for the use of this equipment in industrial sectors where aspects of hygiene, ease of cleaning, and extreme reliability are critical, such as in the food and science sector, as well as in the medical and pharmaceutical industries.
Simple | Complex |
---|---|
If target environments do not require hygienic standards | If cobots with dust and splash protection are required |
If clean room certifications are present | If intended for compatible cleanroom uses |
Programming requirements are directly proportional to the degree to which vision systems are used. It is through AI-powered vision systems that Cobots acquire the “see,” “understand,” and “interpret” skills necessary to perform the tasks assigned to them and interact with human operators.
Applications such as:
- Recognition
- Orientation, positioning, and guidance
- Non-contact measurements
- Verifications
- Classification and selection
- Reading
- Counting
- Surveillance and interaction…
require systems where the crucial factor is the interactions between hardware power (optical detection systems) and information processing capabilities using more or less sophisticated computing, analysis, and matching algorithms.
Simple | Complex |
---|---|
If the interaction is limited to a few devices | If there are random bin-picking algorithms |
If there is limited use of vision systems | If there are monitoring and control sensors |
If the interaction is limited to a few devices |
Main uses / applications
The possible uses of collaborative robots are practically unlimited.
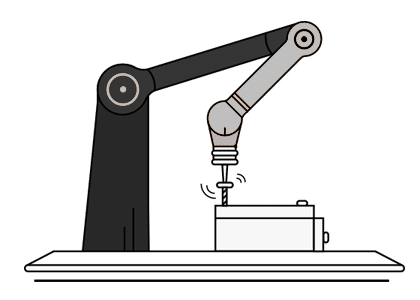
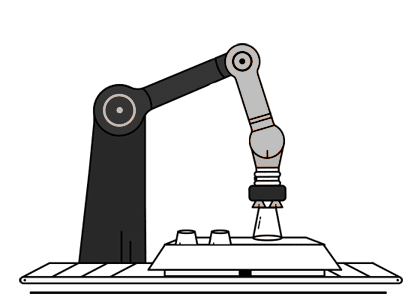
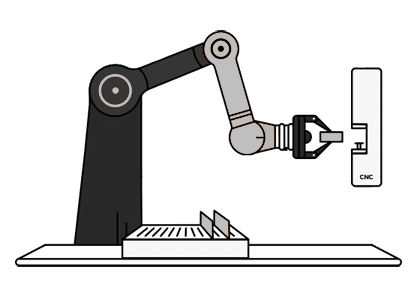
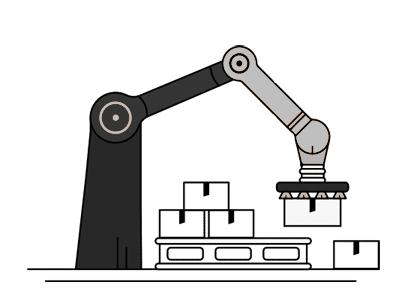
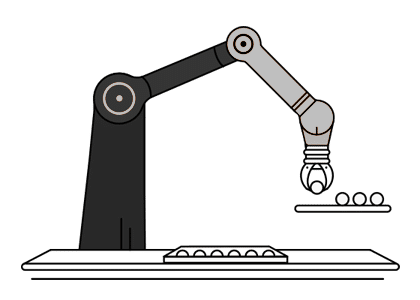
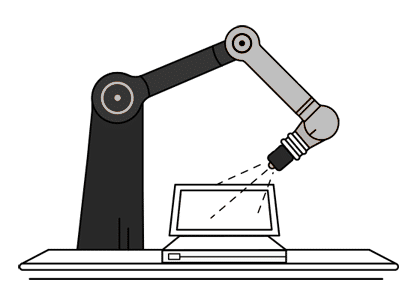
Programing
The latest generation of collaborative robots is very easy to program. It often takes only a few hours of introductory training for an inexperienced user to program the robot independently. Integrated control, user-friendly visualization, and reliable technology make operation extremely easy and flexible.
An integrated controller with digital and analog inputs and outputs generally makes the use of additional devices unnecessary. Instruments, valves, axes, etc. can be connected directly to the control and integrated into the program. Individual controls are not necessary!
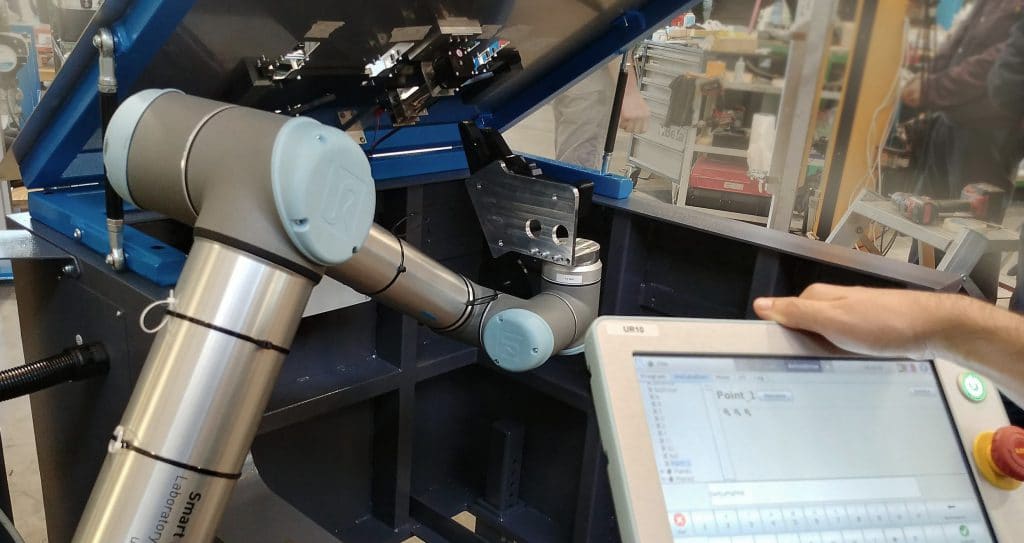
Payback time frame
Due to their low investment and ease of operation, compared to traditional robots, cobots have a shorter time frame and higher ROI, making them ideal for SMEs. They can also be quickly adapted to new tasks.
This is a massive advantage in today’s times in terms of interesting spin-offs of automating new operations, converting to innovative products, and rapidly adjusting production to market demands in terms of volume and the production mix.
Industrial vs collaborative robot comparison (cobot)
If you need to… | …consider industrial robots | …consider collaborative robots |
---|---|---|
High-volume, high-speed production | ||
Productivity similar to that of a human worker | ||
High payload or very long reach, especially at high speed | ||
Program and re-configure the robot internally | ||
Easily reassign the robot to different processes / tasks | ||
Extremely high accuracy, even at high speed | ||
Minimal changes to existing production layout | ||
Have operators access the robot cell to complete tasks | ||
Integration options with other machines and robots | ||
Run processes with few or no employees | ||
Automate processes or products that will not change over time | ||
Low initial cost and payback in less than a year | €€€€€ | €€€ |
Your system integration partner: Carretta
With dozens of deployed robotic systems, we can propose ready-to-use solutions and implement others on a custom-made basis for companies that are seeking to expand and become more competitive.
In 2019 with the WIRE COBOTS project, funded by ESMERA (European SMEs for Robotic Applications H2020-ICT 780265), we were chosen to support EU SMEs in the materialization, testing, and promotion of robotic technologies.
Contact us without obligation!
Please fill in the contact form with your data and we will contact you as soon as possible. Fields marked with * are mandatory.
[ninja_form id=”2″]