Which technologies are the best for the performances in manifacturing?
We present you a curate and still actual (work?) made by McKinsey even if it was published a few years ago. McKinsey is an international consulting company which asked itself which technologies, for the 4.0 Industy, could give the best…
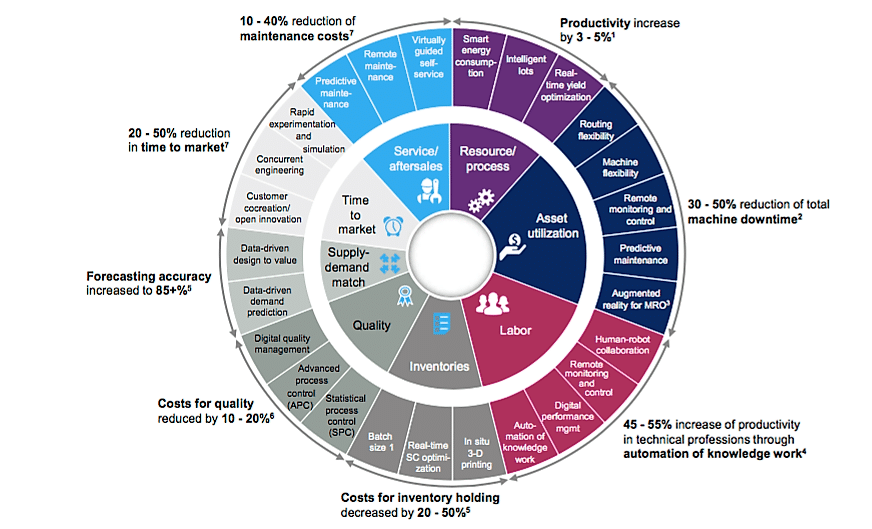
We present you a curate and still actual (work?) made by McKinsey even if it was published a few years ago.
McKinsey is an international consulting company which asked itself which technologies, for the 4.0 Industy, could give the best performance to the businesses.
Starting from the data collected on three hundred manifacturing companies, with the aim of developing an instrument useful to understnd the potential of the 4.0 Industry, McKinsey had “mapped”the eight value drivers with the biggest impact on the performance of a company and, for each one of them, it showed the main levers useful to develop an added value.
The results of this study were summarized at the infographic level in the McKinsey & Company digital compass, 2016.
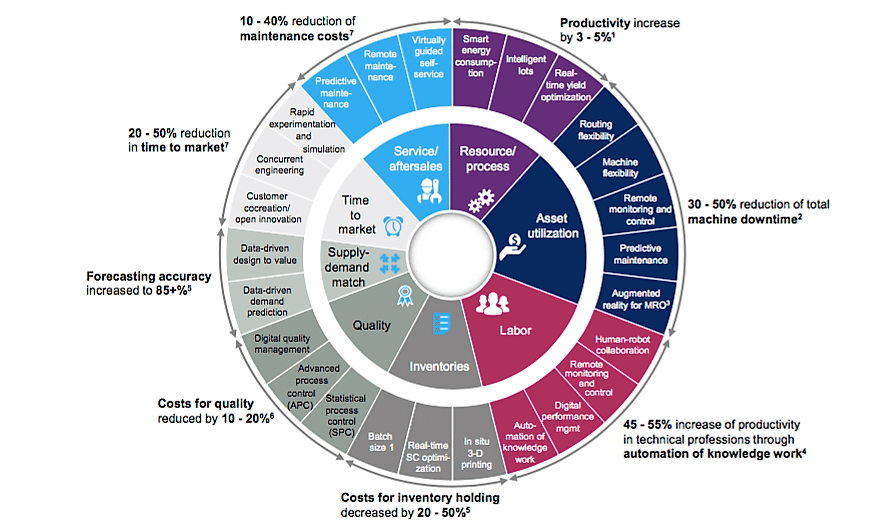
McKinsey’s digital compass. McKinsey & Company, 2016
For McKinsey, the eight areas in which to create value are:
- Resource /Process.
- Asset utilization.
- Labor.
- Inventories.
- Qualiy.
- Supply/Demand match.
- Time to market.
- Service/aftersales.
A really intuitive instrument, useful by everyone, to better decide which are the best technologies to invest on, based on the function or the type of business (value driver).
- Resources and processes.
- Use of corporate assets. In this area, we can find the technological levers in equipments, in the flexible internal logistics, in the remote monitoring, in the predicitive maintenance linked to the Machine Learning tecniques (such as the regression models to predict the remainign life of a machinery a/o classification algorithms to predict a broke in a specific temporal area). Thanks to them, is possible to reduce the time of machine stop to the 50%.
- Work. This area includes all the solutions of the collaborative robotics, remote monitoring, digital performance management and knowledge work utomation (for the McKinsey Global Institute is said “the use of computers to do activities which are based on complex analysis, subtle judgments and creative problem resolution”). The performance of the workers in the 4.0 Industry would increase of the 55%.
- Stock. In this area are inclued equipments for the 3d print and innovative technologies such as the “supply chain’s coordination in real time” and the dinamic redrafting of the lots. The costs for the stock could be decreased up to a 50%
- Quality. This specific area is linked to digital quality management solutions that through the implementation of digital documentation systems help to “notice and memorize the quality, the production and the informations about services”), statistical control of processes and the innovative control of processes, thanks to which is estimated a reduction of the non-quality costs of the 10-20%.
- Meeting between supply and demand. This area includes the methods of data-driven desing to value and of data-driven demand prediction which are about the construction of equipments abilities and a culture that acts based on data. Using this methods, the precision of predictions would increase of the 85%.
- Time-to-market. Are included those solutions which reduce the process that brings to the market, such as the development of parallelal processes (to avoid long and expensive revision processes, many enterprises had started to adopt a development model known as “partially parallel” with a temporal overlap of some phases of the process), sperimentation and virtual simulation, creation of value with costumers and open innovation (innovation routes based on equipments and competences coming from sturtups, universities, research institutes, consultants and companies which are not rivals). In numbers, the advantage of the applicaton is translated in a reduction of the time-to-market up to the 50%.
- Services and post-sale. Here there are all the remote maintenance and predictive maintenance solutions, apart from self-service systems with virtual assistance, able to reduce significantly the assistane costs and maintenance up to the 40%.
Fonte McKinsey & Company, 2016